Pour bénéficier d’un affichage optimal de la boutique en ligne de PanGas, vous avez besoin pour le navigateur de la version minimale suivante:
• Internet Explorer 9.0
• Mozilla Firefox 38
• Safari 8
• Chrome 45
Veuillez vous assurer que JavaScript est activé dans les paramètres de votre navigateur.
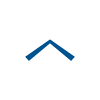
Injection moulding
- Home
- Applications
- Injection Molding, Foaming, Forming & Extrusion
- Injection moulding
Injection molding
Benefit from patented gas technologies developed for injection molding processes
You can increase efficiency and reduce cycle times by using carbon dioxide or nitrogen in gas-assisted injection molding, microcellular foaming or cooling technologies.
Process
Gas Injection Moulding (GID) involves injecting nitrogen at high pressure into the molten polymer to create a hollow part. The GID process provides greater flexibility in designing parts, reduces their weight and allows for savings in raw material costs. Microcellular foam, developed for injection molding, uses carbon dioxide or nitrogen as the blowing agent. The weight of the product is reduced, allowing for significant material savings. In addition, the clamping force of the mold is lower. Cooling the mold with carbon dioxide improves quality and allows for shorter cycle times.
Gas Injection Technology | GID
Use high-pressure nitrogen in your injection molding processes
Your benefits are higher product quality, lower part weight, polymer cost savings and shorter cycle times.
Our supply system includes:
- Optimal supply of single cylinders or bundles of cylinders for testing purposes or in the early stages of production
- Vacuum insulated tanks for liquid nitrogen or carbon dioxide, mainly for industrial production
- On-site nitrogen production with membrane or pressure swing adsorption (PSA) systems
- Nitrogen booster plants
Supply system for gas injection technology (GID): DESY® 300/100
In this pressure feed system, the nitrogen is compressed in liquid state to 290 bar. According to the DESY® 300/100 system, the liquid nitrogen is evaporated in a high-pressure evaporator. For pressure requirements above 300 bar, an additional after-compressor can be used, which then operates with very low energy requirements.
The main advantages of the system are:
- Very low energy consumption thanks to cost-effective compression in the liquid state
- The DESY® 300/100 system pumps exactly the amount of nitrogen required by the user, even with strong fluctuations in demand
- Consistently high quality of injection molded parts thanks to high purity and oil-free nitrogen
Gas injection technology (GID) with internal cooling
If you already use gas injection molding (GID), the internal cooling technology developed by Linde Gas allows you to produce cheaper (thanks to shorter cycle times), lighter and stronger parts. This technology can be applied to any product whose cavity is shaped like a tube. In this process, nitrogen, which is already available for the GID process, flows through the product at high pressure, extracting heat from the inside.
Microcellular foaming
Injection molding or extrusion processes benefit from the use of carbon dioxide or nitrogen in microcellular foaming technology
The weight of the product with a very small and uniform cell structure is significantly reduced. The savings in material are obvious. In addition, the clamping force of the injection molding machine is lower and the cycle time is shorter.
Spot cooling
Do you want to improve the quality of your product while reducing the cooling time during the injection molding process?
Do you want to improve the quality of your product while reducing the cooling time during the injection molding process?
Use the cost-effective and easy-to-install process of cooling with liquid carbon dioxide. This is primarily used to better cool thin or hard-to-cure parts of the mold, such as thin cores. The more uniform cooling of the part can result in huge cooling time savings in practice.